Passinwind
Well-known member
Oh noes, Fig's got a contest going on and the hummingbirds ate my homework. What to do, what to do?
Yeah, that's the ticket. I'll palm off a build from many years ago as something from 2022, no one will be the wiser. Oh wait...that probably won't work out so well. OK, maybe a retrofit to an older build I finished up recently will suffice. I'm only looking to be a playa, not a winner anyway.
So back in the Stoned Ages I decided to try my hand at building a Class D bass amp using an ICEpower module I found used on Diyaudio.com. At the time you needed to be vetted as an OEM by ICE to even buy their stuff from them and they gave you pretty much no tech support if they caught a whiff of DIYer. The guy I bought it from had the right tooling to make me a cable set, which was the next hurdle. This was the 500ASP module, which has been around since the early 00s, was/is quite a bit more expensive than the newer ones, and requires a good bit of finesse to make it suitable for musical instrument builds. I found out later from the US rep that no one else had actually attempted this at that time. Ah well, ignorance is bliss, right?
OK, so I had a power module that had an OK aux power supply that I could run my preamp on, so obviously I decided not to use it, it only does +/-12V, isn't fused, and the audiophile crowd tended to diss it mightily. Fine, I'll buy a separate one from John Broskie's awesome TubeCad website, and then I can run just the preamp for recording or whatnot. I found an old official builder's manual for the power module on some Polish website and figured out what model of toroidal inductors I needed for RFI supression. Spitballed the necessary heatsink size for a fanless build and ordered a custom cut from HeatsinkUSA. Settled on a rack case from Modu in Italy: http://www.modu.it/. I figured on using Front Panel Express for the graphics, who I'd worked with before a few times. Their proprietary software lets you import Inkscape HPGL cutter files directly, you send them the front panel, and it comes back engraved and infilled in a couple of days, like so in the software render, which includes knob mockups:
Found some pretty nice knobs on eBay:
And some killer stepped Noble pots that were NOS Hafler amp pieces. OK, but what about the pie?
I decided on a control fomat of Bass/Mids/Treble with a Baxandall bass/mids section and a Fender-ish separate treble stack. Then a 4th order high pass filter and a one band fully parametric EQ. The first HPF/PEQ board was duff but I have fairly decent rework skills and made it work well enough for proof of concept testing. Here’s the newer set that I finally replaced the old ones with (heh) 8 years later:
Front Panel Express included glued in studs for mounting the preamp boards in a stacked arrangement:
By the time I got this far I was one day out from a big Talkbass GTG in Seattle where I was supplying amps for a friend who was hauling a car load of commercial cab prototypes up from southern Idaho, no pressure or anything. But it all worked and I showed up with it in a janky homemade rack case with the glue still drying, literally:
And a full gutshot:
There's a Jensen input transformer visible at the back just to the right of the heatsink, which is wired straight to the input of the power amp module.
I gigged regularly with this amp for a few years but then built a smaller lighter version using the ubiquitous ICE 700ASC module that is used in many popular 800 watt class bass amps. More on that later. Before I wrap this first book up here are a few sims of the basic PEQ and HPF functionality:
IIRC the PEQ sweep range was something like 100Hz-1.5Khz, the new one is a little more extended both ways now, more like 80-2.6KHz.
More later, I burned through the whole attachment allotment for a single post now.
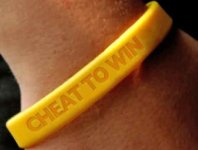
Yeah, that's the ticket. I'll palm off a build from many years ago as something from 2022, no one will be the wiser. Oh wait...that probably won't work out so well. OK, maybe a retrofit to an older build I finished up recently will suffice. I'm only looking to be a playa, not a winner anyway.
So back in the Stoned Ages I decided to try my hand at building a Class D bass amp using an ICEpower module I found used on Diyaudio.com. At the time you needed to be vetted as an OEM by ICE to even buy their stuff from them and they gave you pretty much no tech support if they caught a whiff of DIYer. The guy I bought it from had the right tooling to make me a cable set, which was the next hurdle. This was the 500ASP module, which has been around since the early 00s, was/is quite a bit more expensive than the newer ones, and requires a good bit of finesse to make it suitable for musical instrument builds. I found out later from the US rep that no one else had actually attempted this at that time. Ah well, ignorance is bliss, right?
OK, so I had a power module that had an OK aux power supply that I could run my preamp on, so obviously I decided not to use it, it only does +/-12V, isn't fused, and the audiophile crowd tended to diss it mightily. Fine, I'll buy a separate one from John Broskie's awesome TubeCad website, and then I can run just the preamp for recording or whatnot. I found an old official builder's manual for the power module on some Polish website and figured out what model of toroidal inductors I needed for RFI supression. Spitballed the necessary heatsink size for a fanless build and ordered a custom cut from HeatsinkUSA. Settled on a rack case from Modu in Italy: http://www.modu.it/. I figured on using Front Panel Express for the graphics, who I'd worked with before a few times. Their proprietary software lets you import Inkscape HPGL cutter files directly, you send them the front panel, and it comes back engraved and infilled in a couple of days, like so in the software render, which includes knob mockups:

Found some pretty nice knobs on eBay:
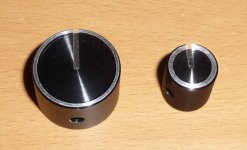
And some killer stepped Noble pots that were NOS Hafler amp pieces. OK, but what about the pie?
I decided on a control fomat of Bass/Mids/Treble with a Baxandall bass/mids section and a Fender-ish separate treble stack. Then a 4th order high pass filter and a one band fully parametric EQ. The first HPF/PEQ board was duff but I have fairly decent rework skills and made it work well enough for proof of concept testing. Here’s the newer set that I finally replaced the old ones with (heh) 8 years later:
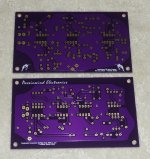
Front Panel Express included glued in studs for mounting the preamp boards in a stacked arrangement:
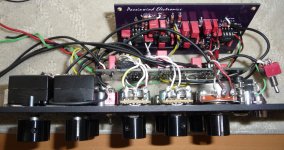
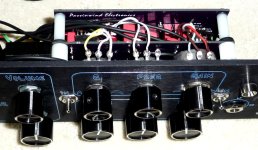
By the time I got this far I was one day out from a big Talkbass GTG in Seattle where I was supplying amps for a friend who was hauling a car load of commercial cab prototypes up from southern Idaho, no pressure or anything. But it all worked and I showed up with it in a janky homemade rack case with the glue still drying, literally:
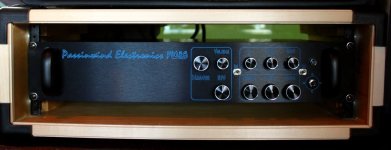
And a full gutshot:
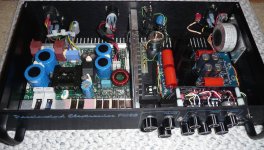
There's a Jensen input transformer visible at the back just to the right of the heatsink, which is wired straight to the input of the power amp module.
I gigged regularly with this amp for a few years but then built a smaller lighter version using the ubiquitous ICE 700ASC module that is used in many popular 800 watt class bass amps. More on that later. Before I wrap this first book up here are a few sims of the basic PEQ and HPF functionality:
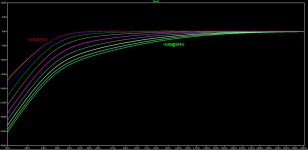
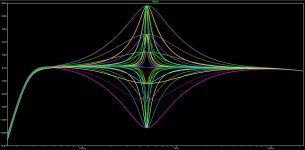
IIRC the PEQ sweep range was something like 100Hz-1.5Khz, the new one is a little more extended both ways now, more like 80-2.6KHz.
More later, I burned through the whole attachment allotment for a single post now.

Last edited: