Cybercow
Well-known member
FWIW, I found these neat little BC modules that will accept +4.5V to +24V and deliver +0.8V to +20V, adjustable with a tiny trimpot. Their output ripple is less than 30mV and the switching frequency is typically 1MHz. We've been using them in a dual rail configuration to deliver ±6V at over 500mA for a Rockman X100 project we've been working on. (see attached image)Seems like someone must already make a 9-18V to +5,+3.3 converter that is reasonably quiet and filtered (and not a linear regulator that would itself consume a lot of power).
Wiring diagram . . . . . . . . . . . . . . . . . . . . The PCB we developed for mounting two of the MP1584EN BC modules . . . .
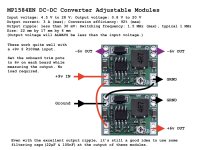
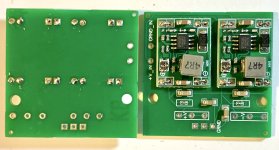