Jovi Bon Kenobi
Well-known member
Hello! This is my method for building a PedalPCB from start to finish. Is it the right way? Not necessarily. It's just what works for me and I hope it sheds some light on certain steps in the process along the way. I created this as a reference guide for anyone to use if needed. Thanks for reading!
Step 1: Drill the enclosure.
I recommend having this done before starting any soldering as it makes test fitting the fully populated board a whole lot easier later.
fig. 1
*Key step* Always print the drill template at 100%. Some printers default to "fit to page". You don't want "fit to page" because the template will be about 5% smaller if you do so...enough for a future struggle.
To attach the template to the enclosure I like using double sided tape. Place the template printed-side down on a flat surface. Put tape on the inside four corners of the drill template face and one in the middle.
fig. 2
With the template tape-side-up on a flat surface I then carefully lower the enclosure down onto it.
fig. 3
Once it's on centered and true fold the four sides of the template flush to the enclosure and secure them with regular tape. Use a center punch or an awl and hammer to mark the holes. I use a step bit and cordless drill to make the holes though a drill press is best. I always start by drilling a little bit where I marked the center to give me a more secure starting point then move to the next until all are done this way. This allows me to eyeball and see if I need to correct my final pass for each hole.
*Side note* After marking the enclosure, some of us like to use a regular drill bit to drill a pilot hole before moving onto the step bit.
fig. 4
Drill all holes then clean up any burrs from drilling with a needle file, if needed. Thoroughly clean inside and out afterwards with a towel and isopropyl alcohol. Optional, compressed air is nice to have to blow out any remaining debris.
fig. 5
Step 1: Drill the enclosure.
I recommend having this done before starting any soldering as it makes test fitting the fully populated board a whole lot easier later.
fig. 1
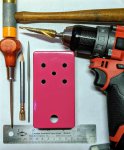
*Key step* Always print the drill template at 100%. Some printers default to "fit to page". You don't want "fit to page" because the template will be about 5% smaller if you do so...enough for a future struggle.
To attach the template to the enclosure I like using double sided tape. Place the template printed-side down on a flat surface. Put tape on the inside four corners of the drill template face and one in the middle.
fig. 2
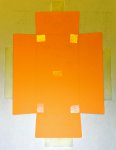
With the template tape-side-up on a flat surface I then carefully lower the enclosure down onto it.
fig. 3
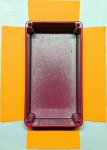
Once it's on centered and true fold the four sides of the template flush to the enclosure and secure them with regular tape. Use a center punch or an awl and hammer to mark the holes. I use a step bit and cordless drill to make the holes though a drill press is best. I always start by drilling a little bit where I marked the center to give me a more secure starting point then move to the next until all are done this way. This allows me to eyeball and see if I need to correct my final pass for each hole.
*Side note* After marking the enclosure, some of us like to use a regular drill bit to drill a pilot hole before moving onto the step bit.
fig. 4
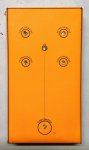
Drill all holes then clean up any burrs from drilling with a needle file, if needed. Thoroughly clean inside and out afterwards with a towel and isopropyl alcohol. Optional, compressed air is nice to have to blow out any remaining debris.
fig. 5
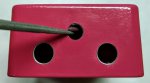
Last edited: