tegendemuur
Well-known member
So, had some moderate success with the Chinese paper last night.
Dollar Gentruhl black nail polish to patch. I accidentally covered one of my dilling holes. Oops.
Also, experimented with adding clear coat to the sides before etching/transferring. I put the enclosure face down and got it with a couple of coats. Then sanded the top flush. Hope is that I won't need to tape the sides of I do that, ultimately saving a step.
Will try and etch it tonight.
View attachment 77848
You are gonna finish it off with pastel colors, yes?
Also, was "The Powermuff Fuzz" too on-the-nose for you?
That series' radiating heart in two colors of pink would make for a neat background as well.
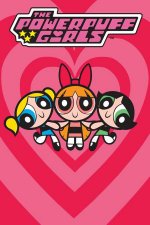