MichaelW
Well-known member
Not really sure if this thread belongs here but it's the only forum that has a "tutorial" badge.
As promised in @BuddytheReow 's parts caster build thread. Here's a method of doing fret level, crown and polishing that's relatively simple and doesn't require a lot of really expensive tools.
I've mentioned before that getting frets right on ANY guitar at ANY price can make or break how a guitar plays.
You WILL require SOME tools. So at a minimum you will need the following:
1. Notched straight edge
You don't have to spend a ton of money on these. I actually have a cheap one from Amazon that does the job.
Here's one.
2. Level Sanding Beam
Again, this is a MUST HAVE but you don't need to spend a ton of money.
I like the style that allows you to level "under the strings". There are times when chasing down fret problems is handy to have one that will work with the strings on. But that's another tutorial for another day.
I like have a longer one and a shorter one but this isn't critical. If you're only going to choose one size, get the 9 inch. It's long enough to be stable doing the whole fret board and short enough for spot leveling certain parts of the neck when necessary.
I have both an expensive StewMac one as well as this cheap one from Amazon. They both work fine.
3. Fret Crowning File or 3 Corner File
Fret crowning files can be ungodly expensive. 3 corner files are cheap but you'll need to grind the edges down so it only cuts on the flat sides.
Or you can get a specialized 3 corner file that has already been ground down.
This is the cheapest "GOOD" fret crowning file if you go that route. $60 investment.
There are cheaper ones but I don't have any experience with them or how good they are.
Before buying a cheapo fret crowning file, I'd spend a couple extra bucks and get the StewMac medium 3 corner file as you can use it for other stuff too. And it does a great job crowning.
4. Fret Rocker
Again you don't need to spend a ton of money on the expensive ones. The cheap ones are fine as long as they are straight.
Here you can get a notched straight edge and fret rocker kit for about $12.
5. Various grits of sandpaper
400, 600, 800, 1000, 1500
So basically, you'll need to invest about ~$80 but these tools will last you pretty much a lifetime. And once you've done your own frets and have your guitar playing like "buttah", you'll wonder how you ever played your other guitars and will be working on them too
This is the neck I'll be working on today. It's a Chinese made Ebay neck. If you've followed my Strato-tele-blaster threads you'll know I've have mixed results with these cheap necks. But this one looks really solid and the frets are well seated. It's quite pretty roasted maple and it was about $50 as I recall.
Here's a closeup of how the fret ends are dressed......meaning they really weren't dressed at all. No big surprise. But what I'm looking for here is any loose frets or frets not completely seated correctly. You'll want to deal with that before starting. Loose frets can be tapped in with a brass or soft hammer.
Or they can be glued and clamped. You can "wick" some super thin superglue along the edges then clamp with two strips of paint stir stick to make sure the ends are nicely glued down. No problems on this neck so we'll move on.
Since this is a maple neck with a finish already applied, I'm going to mask it. I generally don't mask when working on rosewood necks because I'll scrape the fingerboard with a razor blade as a last step to smooth it out. Maple fretboards with or without finish don't scrape easily and wind up looking worse if you do.
So best to protect it while you work. I use plain old painters tape. I got a package with different widths off Amazon.
Ok, this is a bit out of sequence here but before you put masking tape on, you need to make sure the neck is as straight as possible. (As you can see, I forgot before I started masking heh)
What I do is check the function of the truss rod first. I loosen it, and if it's a double action truss rod, make sure it engages in both directions.
Using your notched straight edge while it's loosened check for gaps around the 5th-7th frets. Slowly tighten the truss rod until the gap closes. Try rocking the level, if it rocks then you've gone too far. Back it off a little. Ideally you want no gap and also no rocking. But keep in mind that the neck is made of wood and it won't ever be "perfectly" level. Just get it as close as possible.
With the neck straight, and fretboard masked off, you're ready to start leveling. First use a sharpie and mark the tops of each fret. I like to use the wide sharpies as they cover more evenly.
All marked off here......
Here are my two sanding beams, but for the purposes of this illustration I'm just going to use the longer one. It's a 9" beam. You can buy the special sanding rolls from StewMac and pay big bucks, or you can just do like I did. I got a roll of emery sandpaper 320 grit from Amazon for $7. It doesn't have adhesive on the back, so I just use some double sided tape, stick it on, then trim the edges with a razor blade.
The first few passes with the leveling beam you want to run the full length of the fingerboard, working slowly from side to side following the radius of the fingerboard. You don't want to put a lot of pressure while sanding, usually the weight of the aluminum beam is all you need.
The point here is to make sure you "kiss" every fret and sand off the sharpie marks. The first time you do this you might be alarmed at how much material you're taking off at certain parts of the neck. Don't be, this is normal.
See the pic below where the arrow is pointing at what seems to be a lot of flattening on one fret but the circle shows that there's another fret that hasn't been touched yet. This is the whole point of fret leveling. You want them all the same height at this point.
After a few passes, stop and inspect your progress, go slow. You can always take more material off but you can't put it back on.
What I'm looking for at this point is "low spots". Meaning the sharpie mark hasn't been sanded off yet. Resist the urge to "spot level" that one area, you don't want a "dip" on the frets. Sand the whole fingerboard until all the frets have been touched. The amount taken off each fret will be different, it won't be all uniform.
This is normal, it just shows that the frets were not level.
Continued in next post.
As promised in @BuddytheReow 's parts caster build thread. Here's a method of doing fret level, crown and polishing that's relatively simple and doesn't require a lot of really expensive tools.
I've mentioned before that getting frets right on ANY guitar at ANY price can make or break how a guitar plays.
You WILL require SOME tools. So at a minimum you will need the following:
1. Notched straight edge
You don't have to spend a ton of money on these. I actually have a cheap one from Amazon that does the job.
Here's one.
2. Level Sanding Beam
Again, this is a MUST HAVE but you don't need to spend a ton of money.
I like the style that allows you to level "under the strings". There are times when chasing down fret problems is handy to have one that will work with the strings on. But that's another tutorial for another day.
I like have a longer one and a shorter one but this isn't critical. If you're only going to choose one size, get the 9 inch. It's long enough to be stable doing the whole fret board and short enough for spot leveling certain parts of the neck when necessary.
I have both an expensive StewMac one as well as this cheap one from Amazon. They both work fine.
3. Fret Crowning File or 3 Corner File
Fret crowning files can be ungodly expensive. 3 corner files are cheap but you'll need to grind the edges down so it only cuts on the flat sides.
Or you can get a specialized 3 corner file that has already been ground down.
This is the cheapest "GOOD" fret crowning file if you go that route. $60 investment.
There are cheaper ones but I don't have any experience with them or how good they are.
Before buying a cheapo fret crowning file, I'd spend a couple extra bucks and get the StewMac medium 3 corner file as you can use it for other stuff too. And it does a great job crowning.
4. Fret Rocker
Again you don't need to spend a ton of money on the expensive ones. The cheap ones are fine as long as they are straight.
Here you can get a notched straight edge and fret rocker kit for about $12.
5. Various grits of sandpaper
400, 600, 800, 1000, 1500
So basically, you'll need to invest about ~$80 but these tools will last you pretty much a lifetime. And once you've done your own frets and have your guitar playing like "buttah", you'll wonder how you ever played your other guitars and will be working on them too
This is the neck I'll be working on today. It's a Chinese made Ebay neck. If you've followed my Strato-tele-blaster threads you'll know I've have mixed results with these cheap necks. But this one looks really solid and the frets are well seated. It's quite pretty roasted maple and it was about $50 as I recall.
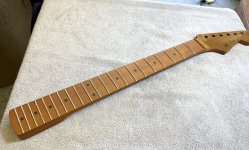
Here's a closeup of how the fret ends are dressed......meaning they really weren't dressed at all. No big surprise. But what I'm looking for here is any loose frets or frets not completely seated correctly. You'll want to deal with that before starting. Loose frets can be tapped in with a brass or soft hammer.
Or they can be glued and clamped. You can "wick" some super thin superglue along the edges then clamp with two strips of paint stir stick to make sure the ends are nicely glued down. No problems on this neck so we'll move on.
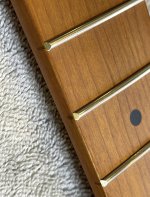
Since this is a maple neck with a finish already applied, I'm going to mask it. I generally don't mask when working on rosewood necks because I'll scrape the fingerboard with a razor blade as a last step to smooth it out. Maple fretboards with or without finish don't scrape easily and wind up looking worse if you do.
So best to protect it while you work. I use plain old painters tape. I got a package with different widths off Amazon.
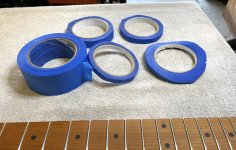
Ok, this is a bit out of sequence here but before you put masking tape on, you need to make sure the neck is as straight as possible. (As you can see, I forgot before I started masking heh)
What I do is check the function of the truss rod first. I loosen it, and if it's a double action truss rod, make sure it engages in both directions.
Using your notched straight edge while it's loosened check for gaps around the 5th-7th frets. Slowly tighten the truss rod until the gap closes. Try rocking the level, if it rocks then you've gone too far. Back it off a little. Ideally you want no gap and also no rocking. But keep in mind that the neck is made of wood and it won't ever be "perfectly" level. Just get it as close as possible.
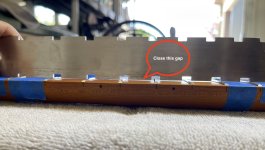
With the neck straight, and fretboard masked off, you're ready to start leveling. First use a sharpie and mark the tops of each fret. I like to use the wide sharpies as they cover more evenly.
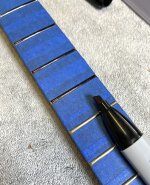
All marked off here......
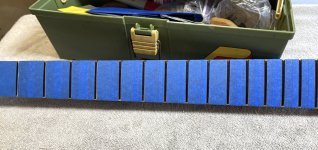
Here are my two sanding beams, but for the purposes of this illustration I'm just going to use the longer one. It's a 9" beam. You can buy the special sanding rolls from StewMac and pay big bucks, or you can just do like I did. I got a roll of emery sandpaper 320 grit from Amazon for $7. It doesn't have adhesive on the back, so I just use some double sided tape, stick it on, then trim the edges with a razor blade.
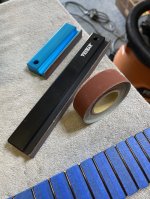
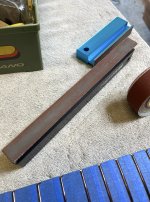
The first few passes with the leveling beam you want to run the full length of the fingerboard, working slowly from side to side following the radius of the fingerboard. You don't want to put a lot of pressure while sanding, usually the weight of the aluminum beam is all you need.
The point here is to make sure you "kiss" every fret and sand off the sharpie marks. The first time you do this you might be alarmed at how much material you're taking off at certain parts of the neck. Don't be, this is normal.
See the pic below where the arrow is pointing at what seems to be a lot of flattening on one fret but the circle shows that there's another fret that hasn't been touched yet. This is the whole point of fret leveling. You want them all the same height at this point.
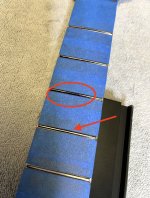
After a few passes, stop and inspect your progress, go slow. You can always take more material off but you can't put it back on.
What I'm looking for at this point is "low spots". Meaning the sharpie mark hasn't been sanded off yet. Resist the urge to "spot level" that one area, you don't want a "dip" on the frets. Sand the whole fingerboard until all the frets have been touched. The amount taken off each fret will be different, it won't be all uniform.
This is normal, it just shows that the frets were not level.
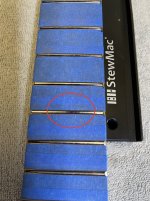
Continued in next post.
Last edited: